PRODUKCJA
Case study: System do zarządzania szwalnią i rozliczaniem akordu
Każde zamówienie było ręcznie analizowane, dane przepisywane, a komunikacja między działami odbywała się przez wiadomości. Jedna pomyłka w rozmiarze lub etykiecie potrafiła zatrzymać cały proces. Ta szwalnia potrzebowała systemu, który w końcu zapanuje nad tym chaosem — bez rewolucji, ale z realnym efektem.
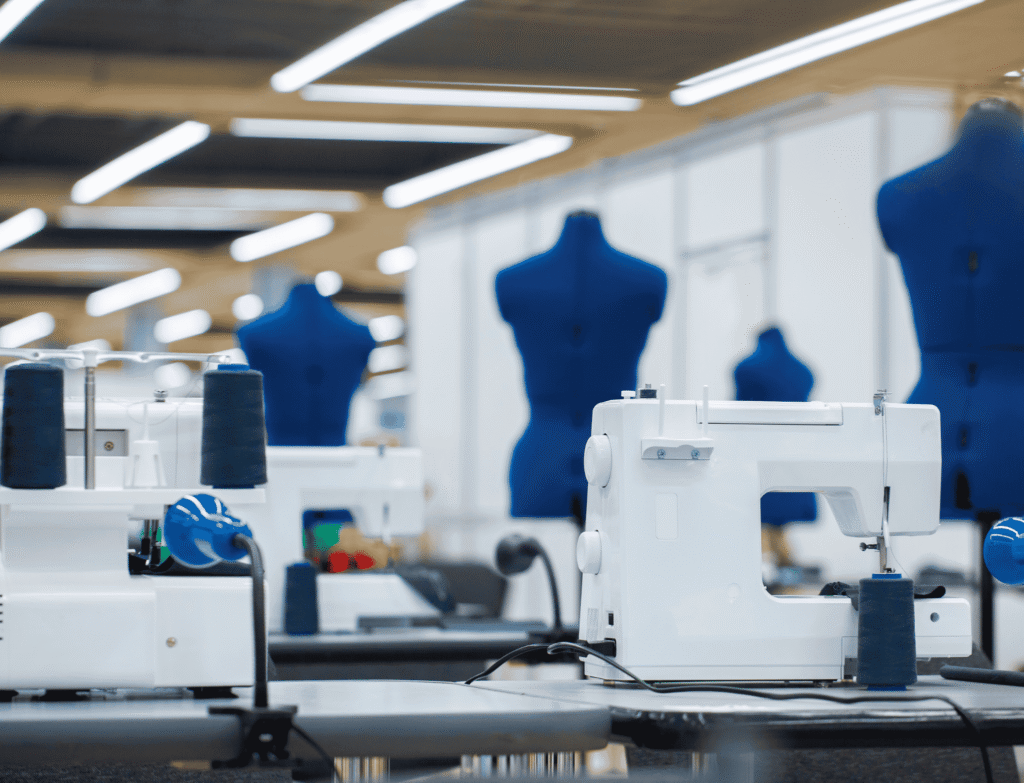
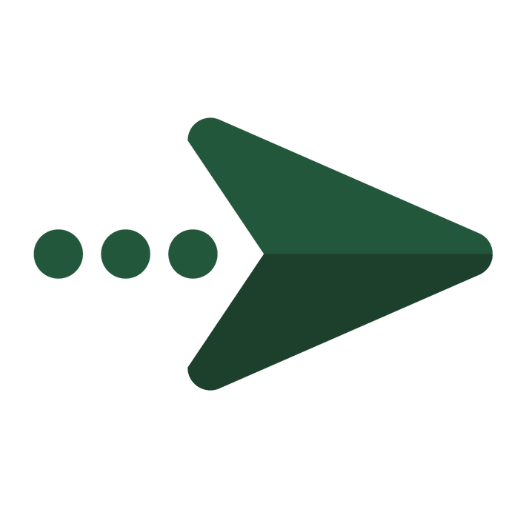
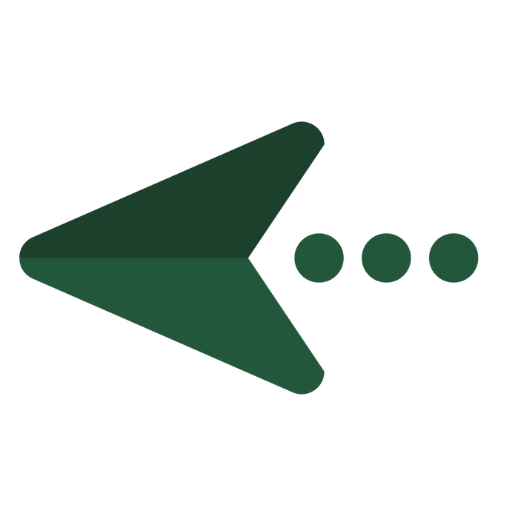
Jak wyglądał proces przed wdrożeniem?
- Zamówienie trafiało do sklepu internetowego. Pracownik ręcznie analizował każde zamówienie i sprawdzał, czy wszystkie elementy kompletu znajdują się na magazynie. Firma sprzedawała zestawy (np. spodnie + bluza), więc jeśli np. na stanie były tylko spodnie, bluza była doszywana.
- Komunikacja z działem krojenia odbywała się przez WhatsApp. Pracownik pisał wiadomość do osoby odpowiedzialnej za krojenie tkanin, często podając ręcznie rozmiary, kolory czy ilości. Nietrudno o pomyłkę – wystarczył jeden źle wpisany rozmiar, by cały proces został zaburzony.
- Nakłady do krojenia były tworzone ręcznie. Osoba krojąca samodzielnie przygotowywała zestawienia do każdego zamówienia. To zajmowało dużo czasu i wymagało ciągłej czujności.
- Wykrój trafiał do krawcowej, która szyć miała „w ciemno”. Po zakończeniu szycia każda krawcowa zapisywała w zeszycie, co uszyła. Dane te były potem zbierane i liczone ręcznie pod koniec miesiąca w celu rozliczenia akordu. Nie było jednak żadnej możliwości sprawdzenia, ile sztuk dana osoba faktycznie uszyła, ani jak długo zajęło jej uszycie konkretnego produktu.
- Pakowanie zamówienia było kolejnym ręcznym etapem. Pracownik działu pakowania musiał najpierw odnaleźć zamówienie w systemie, zidentyfikować, co dokładnie zawiera, ręcznie dobrać odpowiednie sztuki z magazynu, a następnie samodzielnie wydrukować i dopasować etykietę wysyłkową. Pomyłki były częste.
Brzmi znajomo?
Jeśli w Twojej firmie też panuje codzienny chaos, sprawdźmy co możemy uprościć.
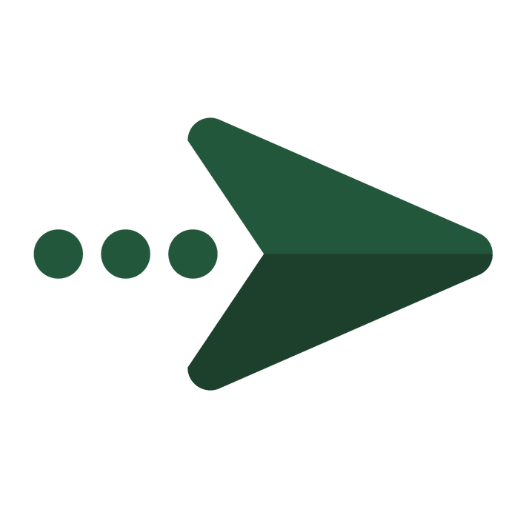
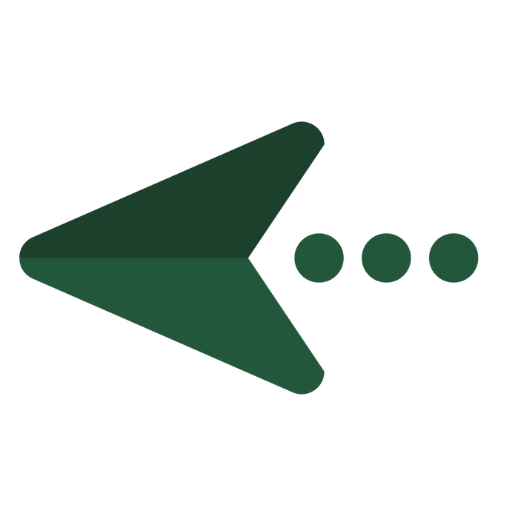
Nasze zadanie: zbudować jeden spójny system, który to wszystko połączy
Etap 1: Automatyzacja zamówień i stanów magazynowych
- Zamówienie trafia do systemu przez API sklepu internetowego – automatycznie, bez udziału człowieka.
- System sam analizuje zawartość zamówienia i sprawdza, czy produkty są dostępne na magazynie.
- Jeśli tak – rezerwuje je i wskazuje ich dokładną lokalizację (np. „regał A, półka 3”).
- Dział pakowania ma swój panel, w którym widzi: co trzeba zabrać, z jakiego regału i do jakiego zamówienia należy dana sztuka.
Etap 2: Automatyzacja krojenia i zarządzania tkaniną
- Elementy, których brakuje na magazynie, trafiają automatycznie do kolejki krojenia.
- System sam generuje nakład do krojenia – kilkanaście zamówień łączone jest w jedną zbiorczą listę optymalizującą zużycie tkanin.
- System automatycznie odejmuje zużytą ilość tkaniny z magazynu i kontroluje stany – jeśli zbliżają się do minimum, właściciel otrzymuje powiadomienie mailowe lub SMS, np. „Zapas materiału X poniżej 10%”.
Etap 3: Produkcja z pełnym śledzeniem i rozliczaniem
- Do każdej skrojonej sztuki drukowana jest etykieta z kodem QR, numerem zamówienia, datą, nazwą produktu i partią. To taki „paszport produktu” – dzięki niemu każda sztuka jest identyfikowalna na każdym etapie.
- Krawcowa korzysta z bardzo prostej, dedykowanej aplikacji na telefon. Skanuje etykietę – system przypisuje konkretną sztukę do konkretnej osoby. Po zakończeniu szycia klika „Uszyte” – system rejestruje: czas rozpoczęcia i zakończenia szycia, dokładny czas pracy nad sztuką, identyfikator krawcowej.
- Aplikacja również monitoruje przerwy w pracy – np. szycie zakończono o 7:52, a następna sztuka rozpoczęta o 8:34 = system rejestruje przerwę 42 minuty. Dzięki temu szef wie nie tylko ile kto uszył, ale również jak wyglądała efektywność i ciągłość pracy.
- Na koniec miesiąca system sam generuje raport akordowy – ile sztuk, ile minut, jakie modele, bez potrzeby ręcznego liczenia. To oszczędność kilkunastu godzin miesięcznie i pełna przejrzystość rozliczeń – bez kontrowersji i wątpliwości.
Etap 4: Automatyzacja pakowania i wysyłki
- Gdy gotowe produkty trafiają na dział pakowania, osoba pakująca skanuje kod QR – na ekranie wyświetlają się wszystkie informacje o zamówieniu.
- System automatycznie drukuje odpowiednią etykietę kurierską, a status zamówienia w sklepie zmienia się na „gotowe do wysyłki”.
- Klient otrzymuje maila z powiadomieniem, a z magazynu automatycznie zdejmowane są: opakowanie foliowe, karton, metka.
- Jeżeli którykolwiek z tych elementów zbliża się do wyczerpania, system wysyła alert, np. „Pozostało tylko 200 opakowań wysyłkowych”.
- Efekt? Oszczędność około 2 godzin dziennie tylko na etapie pakowania.
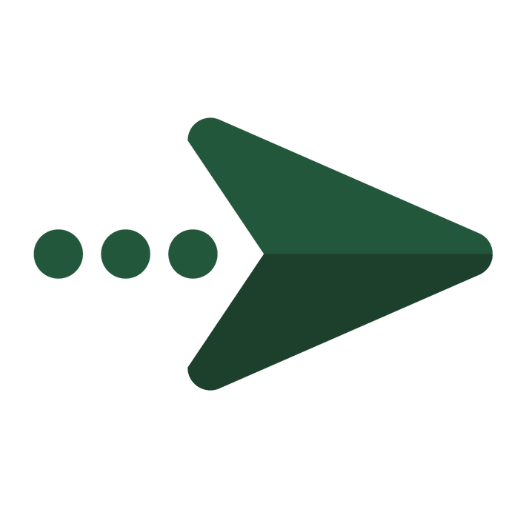
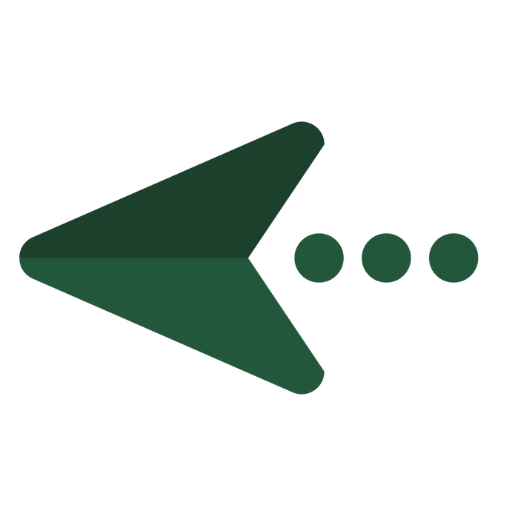
Już w pierwszym dniu działania systemu ta szwalnia odczuła ogromną różnicę:
- Zmniejszenie zatrudnienia z 8 do 7 osób
- Wzrost wydajności: z 60 do 72 sztuk dziennie (+20%)
- Oszczędność czasu: kilkadziesiąt godzin miesięcznie
- Większa kontrola, brak błędów ludzkich, pełna automatyzacja
- Zwrot z inwestycji w ciągu 3 miesięcy
- Czas wdrożenia (projekt + testy + poprawki): 11 tygodni
To wdrożenie pokazało, jak ogromną zmianę może przynieść dobrze przemyślany system – nawet (a może zwłaszcza) w szwalni, gdzie do tej pory wiele rzeczy robiono „na czuja”.
Połączenie automatyzacji, prostoty i przemyślanej obsługi sprawiło, że właściciel zyskał realną kontrolę nad firmą, pracownicy łatwiejszy i sprawiedliwszy system pracy, a klienci – szybszą realizację zamówień i mniej błędów.
Toniesz w ręcznej pracy?
Zrób pierwszy krok, a my przeanalizujemy Twój przypadek i wskażemy najefektywniejszą drogę do uwolnienia czasu w Twojej firmie.